EMR 541A Solar Blind Photomultiplier, with exhaust tip
Photomultiplicateur du type store vénitien
Jalousieform Fotovervielfacher
Manufactured by Electro-Mechanical Research (EMR), Inc. (a subsidiary of Schlumberger Ltd.) -
ASCOP Division (formerly Applied Science Corporation of Princeton), Princeton, N.J.
See also • Voir aussi • Siehe auch :
EMR 541A Solar Blind Photomultiplier
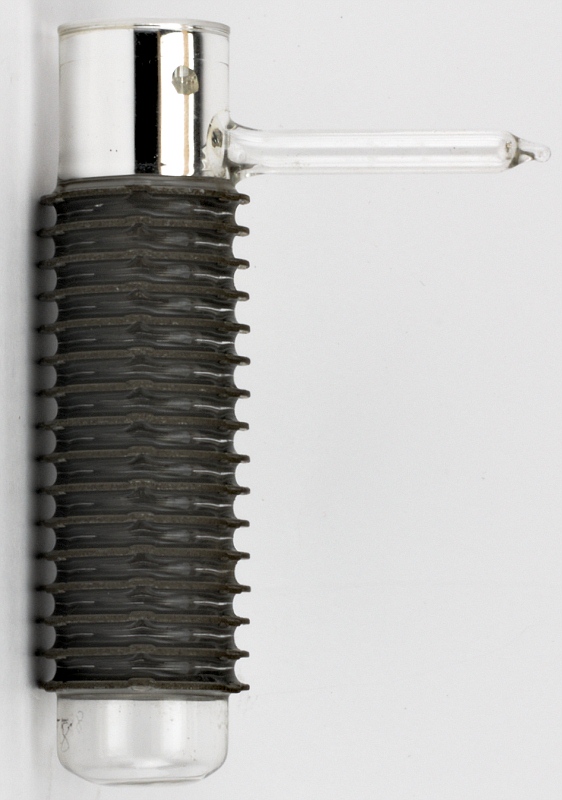
Diamètre • Diameter • Durchmesser : 25 mm • 1"
Longueur • Length • Länge : 92 mm • 3" 5/8
Dave McGuire in Port Charlotte (FL) has the following interesting facts to tell us:
“These tubes were built this way for ruggedness. Though most of EMR's tubes were general purpose
units, they were primarily targeted at two markets: space-borne applications and subterranean oil searches.
In the former application, quite a few EMR PMT's were deployed on various research satellites and probes dating back to
the early 1970's. In the latter application, the tubes can be subjected to corrosive liquids, shock and vibration, and
thermal extremes, including rapid temperature changes. The
Type 510 tube, a much smaller tube employing ceramic rings
instead of glass, is virtually indestructible.
“In oil prospecting, the tubes were typically assembled with a scintillator crystal and an X-ray
generator tube, and sent down into a borehole as a package. I don't know the specific physics behind this, but apparently
oil-bearing rock has different X-ray reflection or excitation characteristics from non-oil-bearing rock, so this package
forms an effective mechanism for oil prospecting.
“My grandmother Ruby (may she rest in peace) worked for EMR in Princeton Junction, NJ, throughout
the 1970s and early 1980s. She was a production group leader in the department that made these 541-series tubes, as well as
the 510 and 575 families. She ran the RF induction heaters that fused the glass and kovar rings together to form the tube
envelope, and inspected the results.
“She worked a lot of overtime, and she used to take me with her for her weekend and after-hours
overtime work when there weren't many other people around. This started when I was about six years old and continued until
I was about twelve.
“Nearly all EMR 541-series tubes were made (well, started... just the glass/kovar envelopes, and
then the photocathode deposition) by my grandmother.
“All 541-family tubes have those exhaust tips (EMR called them “arms”) on them during
manufacture. There should be two, usually 90° apart on the cathode end. One is for pump-down, the other has, for a short
time, what EMR calls a “channel” attached to it. The channel looks like a tube of its own.
“The channel is a bell-shaped glass object about 2 inches long and maybe one inch in diameter.
There is a structure of metal troughs (I suspect these are the actual “channels” for which the whole assembly
is named) containing metallic compounds, with pins on the base to facilitate electrical connections. Current is passed
through those metal structures, heating them and vaporizing the contents of the troughs, and the vaporized compounds are
then deposited on the inside of the front light entry window to form the photocathode.
“After photocathode deposition and final pump-down, a two-headed torch is used to seal the tube
and remove the glass arms. After this, resistors are soldered from kovar ring to kovar ring, to form the voltage divider
for the dynodes.
“As a kid, I got to watch most of the steps in those processes. I didn't understand much of it
back then, but I remember it well.
“It is quite rare to see a “bare” 541 tube like this. As far as I am aware, no tubes
were ever shipped by EMR that weren't completely potted. This suggests that this one may be a production prototype or a
unit sent out for manufacturing quality evaluation.”
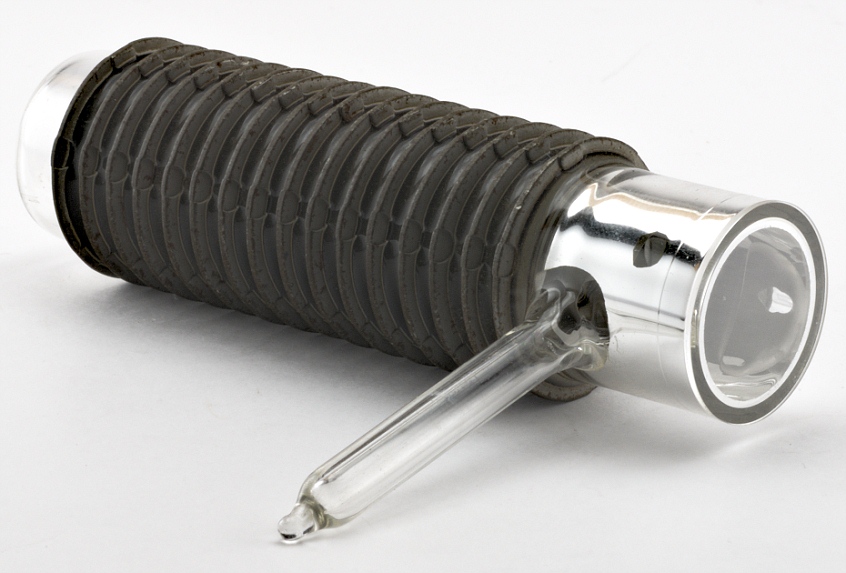
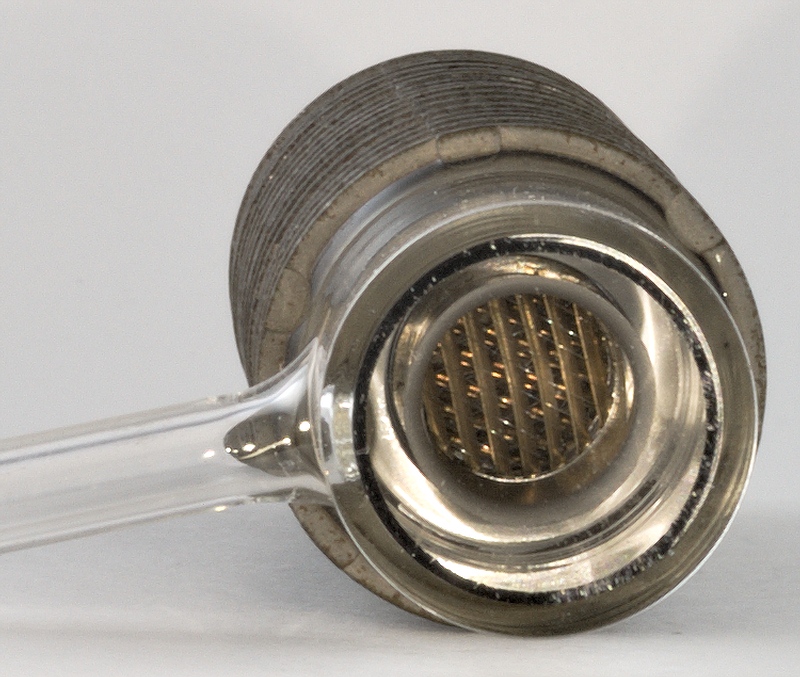
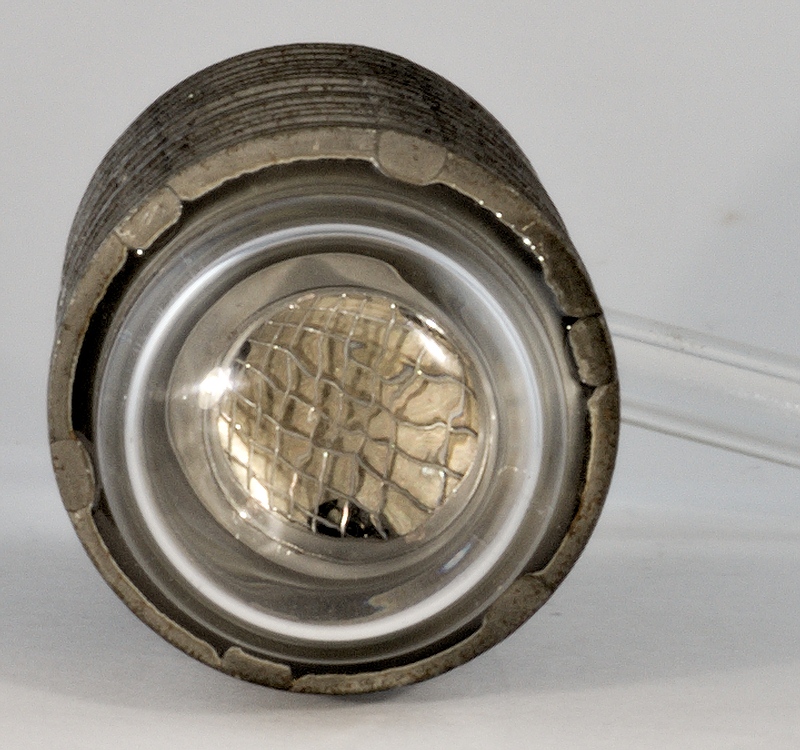
Le contenu de ce site est sous copyleft
The content of this site is under copyleft
Der Inhalt dieser Website steht unter Copyleft